У нас можно недорого заказать курсовую, контрольную, реферат или диплом
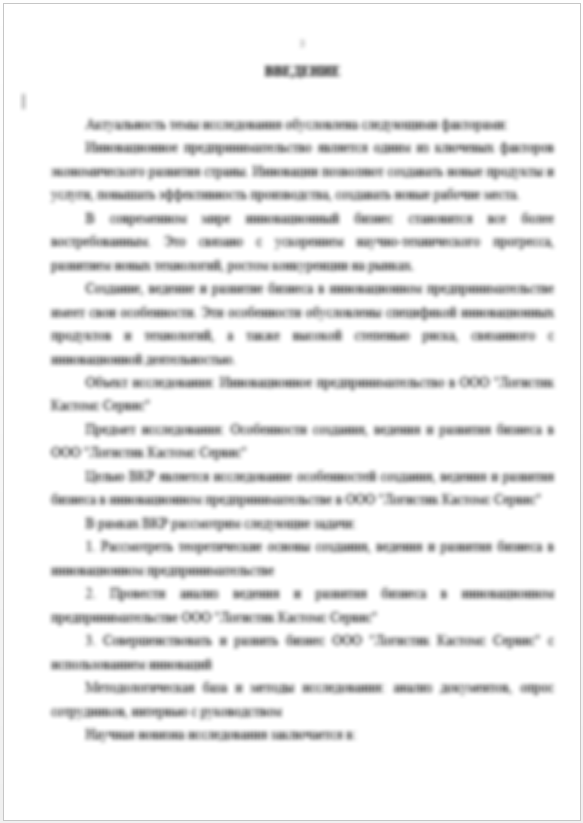
«Монтаж и техническая эксплуатация промышленного оборудования. Z-образный каландр» - Отчет по практике
- 21 страниц(ы)
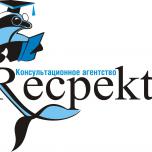
Автор: rezultat
Содержание
Введение 3
1. Технологическая схема цеха 5
2. Характеристика основного оборудования 9
3. Характеристика вспомогательного оборудования 15
4. Монтаж оборудования 16
5. Виды ремонта оборудования и методы его проведения 18
6. Документация на ремонт 20
7. Охрана труда и обеспечение экологической безопасности при эксплуатации и ремонте 21
Введение
ОАО "Омскшина" сегодня является одним из крупнейших предприятий шинной промышленности России по выпуску грузовых, легковых, сельско-хозяйственных и велошин. Официальное решение о строительстве шинного завода в Омске было принято Советом Народных Комиссаров 16 марта 1938 года, а 1 июня вышел в свет Приказ № 422 по Народному комиссариату машиностроения «О строительстве Омского шинного завода в городе Омске». Всего в 1942-1945 гг. Омский шинный выпускал 5 типоразмеров шин, в том числе авиационных, и гусеничные катки для танков. В 1943 году молодое предприятие трижды становилось победителем соцсоревнования среди предприятий Наркомата резиновой промышленности. В 1944-м заводу дважды вручалось Красное знамя Государственного Комитета Обороны СССР.
Продукцией общества оснащаются отечественные и зарубежные автобусы, троллейбусы и грузовые автомобили, легковые автомобили семейства АвтоВАЗ, "Волги", "Москвичи", различные иномарки, сельскохозяйственные и дорожные машины, мотоциклы.
Экономический кризис начала 90-х годов, ставший сложным испытанием для всей российской промышленности, не миновал и ОАО "Омскшина". Однако новому руководству предприятия удалось удержать завод на плаву, сохранив кадровый потенциал и социальную сферу. В 1998 году предприятие налаживает деловые связи с Сибирско-Уральской нефтегазохимической компанией (АК "СИБУР"), а в 1999 году ОАО "Омскшина" входит в состав вертикально интегрированного холдинга "СИБУР", что обеспечивает гарантированные поставки сырья и сбыт продукции.
Началось интенсивное увеличение объемов производства, при этом предприятие продемонстрировало самые высокие темпы роста в отрасли.
Сегодня предприятие предлагает своим потребителям более 100 типоразмеров и моделей шин радиальной и диагональной конструкций для грузовых, легковых автомобилей, сельскохозяйственных машин и велосипедов, около 200 наименований резинотехнических изделий самого разного назначения.
Учитывая требования рынка и новейшие достижения шинной промыш-ленности, специалисты технологических и конструкторских служб предприятия постоянно работают над обновлением и расширением ассортимента выпускаемой продукции, повышением ее качества. В 2002-2003 годах освоено и поставлено на производство 11 новых моделей шин.
Творческий поиск специалистов предприятия направлен на более полное удовлетворение запросов покупателей. Продукция ОАО "Омскшина" отвечает современным требованиям потребителя, она экономична, экологична, обладает современным дизайном, долговечна и надежна.
Все эти свойства омских шин подтверждены не только эксплуатацией и отзывами потребителей, но и временем: на протяжении долгих лет шины с маркой Омского шинного завода, а позже акционерного общества "Омскшина" служили образцом высокого качества.
О качестве продукции ОАО "Омскшина" свидетельствуют российские и международные сертификаты соответствия, многочисленные награды престижных российских и международных выставок и конкурсов.
В конце 2001 года шина модели О-129 для автомобилей "КамАЗ" по итогам Всероссийской программы "100 лучших товаров России" признана лучшей грузовой шиной страны, а в 2002 году - уже легковая шина - 175/70R13 мод. О-144 стала лауреатом этого конкурса.
В феврале 2003 года за шины мод. О-143 для автомобилей ВАЗ предприятию вручен диплом I степени и золотая медаль конкурса "Лучшая автомобильная шина на дорогах России", который ежегодно проводится в рамках Международного специализированной ярмарки "Шины, РТИ и каучуки". Серебро этого конкурса еще у двух омских шин - мод. О-144 и О-164. В мае 2003 года продукция ОАО "Омскшина" была отмечена высшей наградой VIII специализированной выставки "Автосалон" - золотой медалью за создание и успешное внедрение новейших технологий в производстве шин для отечественных автомобилей.
Завод входит в число 200 крупнейших предприятий России по объёму реализации продукции в рейтинге, по данным «Эксперт РА».
Выдержка из текста работы
Каландр транспортируют заказчику в специальной упаковке. Перед монтажом проверяют размеры фундамента, расположение и глубину колодцев под фундаментные болты. 3aтем на фундамент устанавливают фундаментную плиту и очищают ее обработанные поверхности. После этого выверяют плиту на горизонтальность в продольном и поперечном направлениях по поверочной линейке и уровню. Выставляют плиту с помощью подкладок из полосовой стали.
При установке станин на плите выверяют их вертикальность, регулируя подведением подкладок под подошвы станины. Расстояние между внутренними направляющими правой и левой станин должно быть отрегулировано с точностью ±0,5 мм при непараллельности между ними 0,2 мм на всю длину обработанных платиков (мест прилегания корпусов задних подшипников). С помощью линейки станины выводят в одну плоскость. После этого монтируют задний и передний валки в сборе с подшипниками, проверяют плотность их прилегания.
После этого вторично проверяют точность монтажа, затем заливают фундаментные болты, насаживают приводную и фрикционные шестерни, одновременно устанавливают привод.
Далее производят центровку валов редуктора и электродвигателя, устанавливают тормоз, работу которого проверяют на холостой обкатке. Устанавливают механизмы регулировки зазора.
После повторной контрольной проверки соединений и зацеплений производят окончательную затяжку болтов крепления станины, выносного подшипника, редуктора привода и электродвигателя.
Затем собирают систему охлаждения и нагрева, устанавливают ограничительные стрелки для валков.
После установки аварийного устройства монтируют систему смазки, устанавливают ограждения, конечные выключатели.
После монтажа сначала испытывают охлаждающую и смазывающую системы. Систему циркуляционной смазки проверяют на герметичность, качество промывки и степень заполнения. Промывку ведут до тех пор, пока промывная смесь, состоящая из 50% керосина и 50% масла «Индустриальное-20», не будет выходить из системы чистой, без грязи и осадка. После этого систему заполняют свежим маслом до тех пор, пока оно не начнет выходить из концов трубок в месте их присоединения к точкам смазки. Только тогда можно присоединять трубопроводы.
Заполнение смазкой подшипников, редуктора и других узлов производят согласно карте смазки.
Во время сборки необходимо уделять внимание узлу валковых подшипников: в соединениях не должно быть коррозии, задиров, заусенцев.
Все смазочные отверстия продувают воздухом с предварительной их прочисткой.
Величина радиального зазора между втулкой подшипника и шейкой вала должна быть в пределах 0,5-0,9 мм.
Правильность сборки механизма регулировки зазора проверяют путем трехкратного сближения и раздвижения валков.
Обкатку на холостом ходу проводят в течение 48 часов. Во время обкатки проверяют:
1 – работу аварийного устройства и эффективность торможения путем измерения пути, пройденного любой точкой поверхности переднего валка после нажатия на конечный выключатель; при этом путь ее не должен превышать 0,5 оборота;
2 – плавность работы всех узлов и механизмов, действие конечных вы-ключателей;
3 – замеряют мощность.
После обкатки вхолостую и устранения обнаруженных дефектов производят обкатку вальцев под нагрузкой в течение 48 часов. Нагрузку постепенно увеличивают, к концу обкатки она должна достигнуть номинальной величины.
Правильность монтажа характеризуют следующие признаки:
1 – отсутствие ударов и вибрации машины;
2 – бесшумность работы зубчатых передач при прямом и обратном ходе;
3 – температура подшипников валков при холостом ходе не выше 30 градусов, а под нагрузкой до 60 гоадусов;
4 – безотказная работа всех устройств, особенно аварийного выключателя и механизма регулировки зазора валков;
5 – отсутствие видимых осевых перемещений валков и валов при прямом и обратном их вращении.
Сдача в эксплуатацию производится по существующей форме. Демонтаж осуществляется в последовательности, обратной монтажу. Используемые при этом такелажные механизмы – домкрат грузоподъемностью 50-100 т, тали.
Заключение
Для обеспечения безопасных условий обслуживания каландров и других валковых машин необходимо предусмотреть ограждение всех вращающихся деталей, а также установить надежный в работе аварийный выключатель для мгновенной остановки машины.
Каландр является мощной машиной, опасной для работающих, поэтому он должен быть снабжен предохранительными устройствами. Наибольшая опасность - это попадание руки работающего в зазор между валками. Главным средством, обеспечивающим безопасность работающих, является система аварийной остановки каландра. В случае необходимости каландр должен быть остановлен на полном ходу, причем под нагрузкой он должен остановиться практически мгновенно, а при работе вхолостую проворачивание валков после воздействия на аварийный останов должно быть не более 1/4 оборота.
Для аварийного останова вдоль валков спереди и сзади каландра имеется штанга или тросик, соединенный с переключателем, включающим систему аварийной остановки в работу. В ряде современных каландров кроме ручного аварийного останова каландра предусматривается также аварийный останов от нажатия ногой на дополнительное аварийное устройство, расположенное в нижней части станины. В каландрах старых конструкций в том случае, если привод осуществляется от электродвигателя переменного тока, применяется специальный колодочный тормоз. Все современные каландры выпускаются с приводом от электродвигателей постоянного тока. В этом случае применяется электродинамическое торможение.
При нажатии с определенным усилием на трос или штангу человек от-ключает электродвигатель привода машины от источника тока. Для торможения и остановки деталей привода, продолжающих вращаться по инерции, используют так называемые электромеханические и электродинамические способы торможения. При электродинамическом торможении после воздействия на тросе или штангу отключается электродвигатель привода машины, одновременно включается электромагнит колодочного тормоза, далее под действием груза и системы рычагов колодки тормоза обжимают муфту и останавливают продол-жающий вращение по инерции приводной вал машины. Одновременно с от-ключением электродвигателя привода производится переключение электрической цепи и создается электродинамический момент, вращающий якорь электродвигателя в обратном направлении. Качество работы механизма аварийной остановки валковых машин определяется длиной дуг поворота валков после отключения электродвигателя при незагруженных валках. Длина дуги поворота валков после отключения двигателя не должна превышать 1/4 части оборота валка.
Примечания
без графической части
шрифт 14, интервал 1
Тема: | «Монтаж и техническая эксплуатация промышленного оборудования. Z-образный каландр» | |
Раздел: | Разное | |
Тип: | Отчет по практике | |
Страниц: | 21 | |
Цена: | 700 руб. |
Закажите авторскую работу по вашему заданию.
- Цены ниже рыночных
- Удобный личный кабинет
- Необходимый уровень антиплагиата
- Прямое общение с исполнителем вашей работы
- Бесплатные доработки и консультации
- Минимальные сроки выполнения
Мы уже помогли 24535 студентам
Средний балл наших работ
- 4.89 из 5
написания вашей работы
Не подошла эта работа?
Воспользуйтесь поиском по базе из более чем 40000 работ
-
Контрольная работа:
Участие адвоката при рассмотрении дел в административном производстве.
10 страниц(ы) 2011 2375
-
Курсовая работа:
Электроэнергетика. ПРОЕКТИРОВАНИЕ ЭЛЕКТРИЧЕСКИХ СЕТЕЙ ЭНЕРГОСИСТЕМ
35 страниц(ы) 2010 2950
-
Курсовая работа:
40 страниц(ы) 2011 4308
-
Курсовая работа:
Метрология, стандартизация и сертификация. Вариант 12
35 страниц(ы) 2013 808
-
Дипломная работа:
Индивидуально-психологические особенности как фактор выбора профессии
125 страниц(ы) 2013 678
-
Курсовая работа:
Равновесие в модели Дж. Хикса «IS-LM»
22 страниц(ы) 2011 2588
-
Контрольная работа:
Система арбитражных судов. Банкротство
12 страниц(ы) 2011 2360
-
Контрольная работа:
Квалификация преступлений. Вариант № 8
10 страниц(ы) 2013 605
-
Дипломная работа:
Конституционные права и обязанности человека и гражданина. Гарантии и способы обеспечения
64 страниц(ы) 2012 2935
-
Контрольная работа:
Образование Древнерусского государства. «Русская Правда» и ее редакции
24 страниц(ы) 2013 847
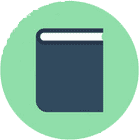
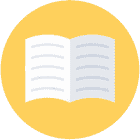
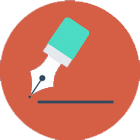
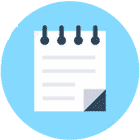
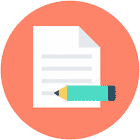
682 автора
помогают студентам
23 задания
за последние сутки
10 минут
среднее время отклика
-
Отчет по практике:
Монтаж и техническая эксплуатация промышленного оборудования. Резиносмеситель РДВС
20 страниц(ы) -
Дипломная работа:
Фундаментальный и технический анализ
81 страниц(ы) -
Курсовая работа:
Анализ организационного устройства (АОУ) учреждения образования
33 страниц(ы) -
Дипломная работа:
Методы и технические средства диагностирования магистральных нефтепроводов
92 страниц(ы) -
Курсовая работа:
Расчет и подбор машины взбивальной
23 страниц(ы)