У нас можно недорого заказать курсовую, контрольную, реферат или диплом
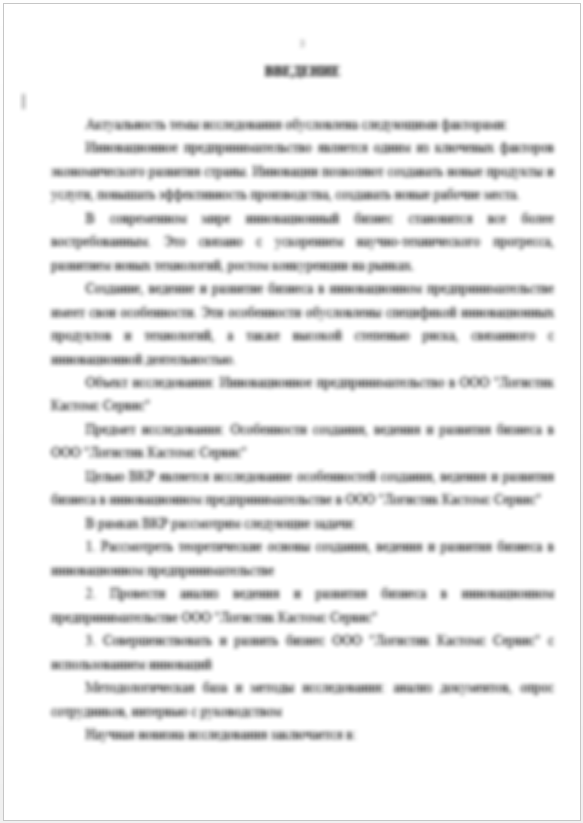
«Технологический процесс производства валов длиной 1000 мм и диаметром 150 мм (вал ответственного назначения)» - Контрольная работа
- 16 страниц(ы)
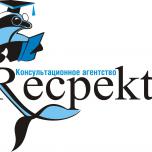
Автор: rezultat
Содержание
Опишите технологический процесс производства валов длиной 1000 мм и диаметром 150 мм (вал ответственного назначения)
-Исходные материалы для получения чугуна
-Подготовка руд к доменной плавке
-Исходные материалы для получения стали
-Получение заготовки вала ковкой
-Термическая обработка
Задача 1.
Зубчатые колеса в зависимости от условий работы и возникающих напряжений можно изготавливать из стали обыкновенного качества, качественной углеродистой и легированной с различным содержанием легирующих элементов. Выберите, руководствуясь техническими и экономическими соображениями, сталь для изготовления колес диаметром 50 мм и высотой 30 мм с пределом текучести не ниже 360.380 МПа. Укажите термическую обработку колес, механические свойства и структуру выбранной стали в готовом изделии и для сравнения механические свойства и структуру сталей 45 и 40ХН после улучшающей термической обработки.
Задача 2.
Выберите сталь для червячных фрез, обрабатывающих конструкционные стали твёрдостью НВ 220.240. Объясните причины, по которым для этого назначения нецелесообразно использовать углеродистую сталь У12 с высокой твёрдостью (63.65 НRС). Рекомендуйте режим термической обработки фрез из выбранной быстрорежущей стали, приняв, что фрезы изготовлены из проката диаметром 40 мм. Опишите получаемую структуру и возможный комплекс эксплуатационных свойств.
Задача 3
Выберите марку стали для изготовления крепёжных болтов, если их обрабатывают на быстроходных станках-автоматах, на которых надо обеспечить максимальную производительность резания и получить высокую чистоту обрабатываемой поверхности; болты не воспринимают в конструкции значительных нагрузок, но работают в агрессивной среде. Укажите марку, химический состав, механические свойства и назначение стали этого типа. Объясните влияние отдельных элементов, присутствующих в этой стали, на формирование заданного комплекса эксплуатационных свойств.
Приведите для сравнения состав, структуру и механические свойства цветного сплава высокой обрабатываемости, применяемого для аналогичного назначения. Объясните, в каких случаях следует применять тот или иной из выбранных материалов и почему.
Введение
Для изготовления наиболее ответственных деталей, для которых требуется материал особой прочности в крупных сечениях, используются легированные стали - хромоникельмолибденованадиевые. Примерами таких деталей являются: поковки валов и цельнокованных роторов турбин, валы высоконапряженных трубовоздуходувных машин, детали редукторов и т.д. Для работы в указанных условиях наиболее подходит материал – сталь
36Х2Н2МФА (легирующими элементами в данной стали являются Cr, Ni, Mo, и V), т.к. она обладает высокой прочностью, пластичностью и вязкостью и низким порогом хладноломкости. Буква - А означает сталь высококачественная (с низким содержанием вредных примесей). Этому способствует высокое содержание никеля.
Молибден, присутствующий в стали, повышает ее теплоемкость. Эту сталь можно использовать при 400-500 °С. Также данная сталь обладает высокой прокаливаемостью (критический диаметр свыше 100 мм), что позволяет упрочнять термической обработкой крупные детали. Даже в очень больших сечениях (1000 – 1500 мм и более) в сердцевине после закалки образуется бейнит, а после отпуска сорбит. Недостатками высоколегированных хромоникельмолибденованадиевых сталей являются трудность их обработки резанием и большая склонность к образованию флокенов. При их обнаружении бракуют всю партию поковок. Также данные стали являются дорогими и их следует применять только в том случае если более дешевые стали не обеспечивают требования, предъявляемые к изделию.
Выдержка из текста работы
Исходные материалы для получения стали
• Металлошихта: жидкий или твердый чугун, скрап (стальной, чугунный лом, стружка, обрезки), ферросплавы.
• Флюсы: известняк, марганцевая руда.
• Окислители: железная руда, кислород, воздух.
Задача передела чугуна в сталь состоит в том, чтобы из чугуна удалить избыток углерода, кремния, марганца и др. примесей.
В металлургии в основном применяют следующие способы получения стали: кислородно- конверторный, мартеновский, электротермический.
Для производства высококачественных легированных сталей используют два основных способа: кислый мартеновский процесс и выплавка в электродуговых печах.
В мартеновских печах при выплавке легированных сталей, когда в ванну вводят значительное количество ферросплавов, охлаждается металл. Из-за трудности нагрева металлической ванны количество одновременно присаживаемых ферросплавов ограничивают 3% массы металла. Поэтому высоколегированные стали, за редким исключением, в мартеновских печах не выплавляют. Избегают выплавлять и стали с повышенным содержание тугоплавких элементов (вольфрам, молибден). Кроме этих недостатков, данный процесс обладает другими: экологические, опасность разрушения при охлаждении печи. В настоящее время, по ряду определенных причин, от данного способа получения стали отказываются.
Плавильные электропечи имеют преимущества по сравнению с другими плавильными агрегатами, так как в них можно получать высокую температуру металла, создавать окислительную, восстановительную, нейтральную атмосферу и вакуум, что позволяет выплавлять сталь любого состава, раскислять металл с образованием минимального количества неметаллических включений – продуктов раскисления. Поэтому электропечи используют для выплавки конструкционных, высоколегированных, инструментальных, специальных сталей и сплавов.
Нам необходимо получить высококачественную легированную сталь 36Х2Н2МФА, где "36" - среднее содержание углерода в сотых долях процента. Такую сталь целесообразнее получить в электродуговых печах.
Сущностью любого металлургического передела чугуна в сталь является снижение содержания углерода и примесей путем их избирательного окисления и перевода в шлак и газы в процессе плавки.
Заключение
Для устранения физической и химической неоднородности (сорбит, троостит, бейнит или мартенсит) и, как следствие, высокой твердости, созданных предыдущей обработкой, используют отжиг.
(слоистый излом) и флокены (тонкие внутренние трещины, наблюдаемые в изломе в виде белых овальных пятен). Нагрев при отжиге 1100 – 1200°С, так как только в этом случае более полно протекают диффузионные процессы, необходимые для выравнивания состава стали.
Общая продолжительность отжига (нагрев, выдержка и медленное охлаждение) больших садок металла достигает 5 – 100 ч. и более. В зависимости от состава стали и массы садки продолжительность выдержки составляет 8 – 20 ч.
После проведения отжига заготовка подвергается механической токарной, (шлифовальной) обработке, с помощью которой получаются окончательные размеры вала. Затем вал подлежит закалке и высокому отпуску. Закалка применяется для повышения прочности, твердости, получения достаточно высокой пластичности и вязкости, а для ряда деталей – высокой износостойкости.
Закалка - термическая обработка, заключающаяся в нагревании стали до температуры растворения избыточных фаз, выдержке и последующем охлаждении.
После закалки проводят отпуск – нагрев закалённой стали с последующим охлаждением с определённой скоростью. Это окончательная операция термической обработки, в результате которой сталь получает требуемые механические свойства.
Список литературы
1. Фетисов Г.П. и др. Материаловедение и технология металлов. учебник. – М.: Высшая школа, 2001. 635 с.
2. Пейсахов и др. Материаловедение и технология конструкционных материалов. – С-Пб.: Издательство Михайлова В.А., 2005. 410 с.
3. Материаловедение. Технология конструкционных материалов. – под редакцией В.С. Чередниченко. – М.: Идел-Пресс, 2006. 752 с.
Тема: | «Технологический процесс производства валов длиной 1000 мм и диаметром 150 мм (вал ответственного назначения)» | |
Раздел: | Материаловедение | |
Тип: | Контрольная работа | |
Страниц: | 16 | |
Цена: | 700 руб. |
Закажите авторскую работу по вашему заданию.
- Цены ниже рыночных
- Удобный личный кабинет
- Необходимый уровень антиплагиата
- Прямое общение с исполнителем вашей работы
- Бесплатные доработки и консультации
- Минимальные сроки выполнения
Мы уже помогли 24535 студентам
Средний балл наших работ
- 4.89 из 5
написания вашей работы
Не подошла эта работа?
Воспользуйтесь поиском по базе из более чем 40000 работ
-
Дипломная работа:
Проектирование шаблонов сети малого предприятия
38 страниц(ы) 2012 1788
-
Контрольная работа:
Теория финансового менеджмента. Оценка стоимости бизнеса
19 страниц(ы) 2011 1994
-
Реферат:
Анализ развития формы шкафа в исторической ретроспективе
18 страниц(ы) 2011 2779
-
Курсовая работа:
31 страниц(ы) 2012 2561
-
Контрольная работа:
8 страниц(ы) 2013 1398
-
Контрольная работа:
15 страниц(ы) 2012 1995
-
Контрольная работа:
6 страниц(ы) 2011 2248
-
Контрольная работа:
13 страниц(ы) 2012 3652
-
Контрольная работа:
Переработка нефти и газа. РАСЧЕТ ВОДООЧИСТНОЙ УСТАНОВКИ
12 страниц(ы) 2012 2197
-
Дипломная работа:
Экологическая экспертиза почв Оконешниковского района Омской области
74 страниц(ы) 2011 3522
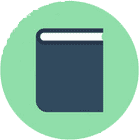
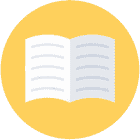
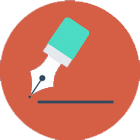
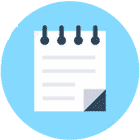
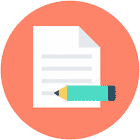
682 автора
помогают студентам
23 задания
за последние сутки
10 минут
среднее время отклика